Manufacturing Process Of Acetate Frame
What kind of glasses are the most popular now? Yes, they are plate glasses. Plate glasses are one of the most popular glasses at present. The main component of the panel is acetate fiber, which has been proved to be the ideal material for manufacturing acetate sunglasses frame due to its rich color, stability and diversity of processing technology. Acetate Optical and Acetate Sunglasses made of acetate fiber have moderate weight, rich colors, various styles and structures. Especially, the glasses made of metal and other different materials are popular with consumers. This paper mainly introduces the production process of plate glasses.
One:Depot line
1. Cutting: cut raw materials into blocks of required length and shape.
2. Fine carving of inner and outer rings: according to the size and model required by the order or the engineering drawing, the inner and outer rings are carved with CNC, so that the basic shape of the front frame of the glasses can be obtained.
3. Combination of materials (Zhuangtou, Ye): The purpose of combination of materials is to put Zhuangtou and Ye on the shelf with the inner and outer rings already finished. Dip the head, leaves and shelf into the potion. When putting together the head and leaves, first pick up the shelf and put it in place, then put the head or leaves on the shelf as required. Put the frame of the assembled head into the air compressor for pressure.
4. Manual. Grind the shelf manually with a file, blade and filing board to make it smooth and free of knife marks.
5. Bend the ring, heat the shelf, and bend the shelf to the proper bending. Put the bent frame into ice water to cool it quickly to prevent it from rebounding and recovering. In this way, the previous process of the front frame is basically completed.
6. Spleen pre process: Spleen cutting, spleen planing, spleen gong, bronze needle making, slingshot cover making, scraping, marking, filing, etc.
7、 Grinding part. After the previous process of front frame and spleen is completed, the subsequent processes such as paulownia rolling, nail reaming and polishing will be started.
8. Wash and polish. Wash, polish and dry the finished rings and rings in the ultrasonic machine. Soak the blow dried rings and in acetone, wash the dead corners and corners smooth, and then blow them dry
9. Guntong: Mix the washed and polished ring or ball with wood grain, and then put it into the roller to make it smooth and shiny.
Second: Assembly line:
1. Nail hinge: Nail the hinge into the ring so that it can be combined with the hinge and remove the glue mark near the hinge. 2. Cutting: cut the ring and ring nailed with the hinge as required to facilitate the combination of the ring and ring. 3. Drilling machine pattern. 4. Screwing: fix the cut ring and 肶 with screws. 5. Filing head: manually operate the rack after screwing to make it smooth and round. 6. Install horn flowers.
Three: Packaging line:
1. Car piece 2. Pad printing: print the required characters on the lens frame. 2. Film mounting: Install the finished lens into the lens frame. 3. Holder: reshape and check the whole lens holder for big and small edges and high and low angles; Check whether the screws are crooked or loose; Whether the ring is warped; Bending of 肶 and 肶; Openness; Overall inspection; Polish the mirror frame after inspection. 4. Packaging: wipe the frame and smear, wrap the lens in a bag, attach a protective film and label to the lens, put the glasses in a bag, box and box.
Four: Transportation. According to the requirements of our guests, since most of our guests are medium and high-end glasses brands, and the glasses are not cheap, most of our customers use express or air transportation to ensure that the products are delivered to customers quickly and safely.
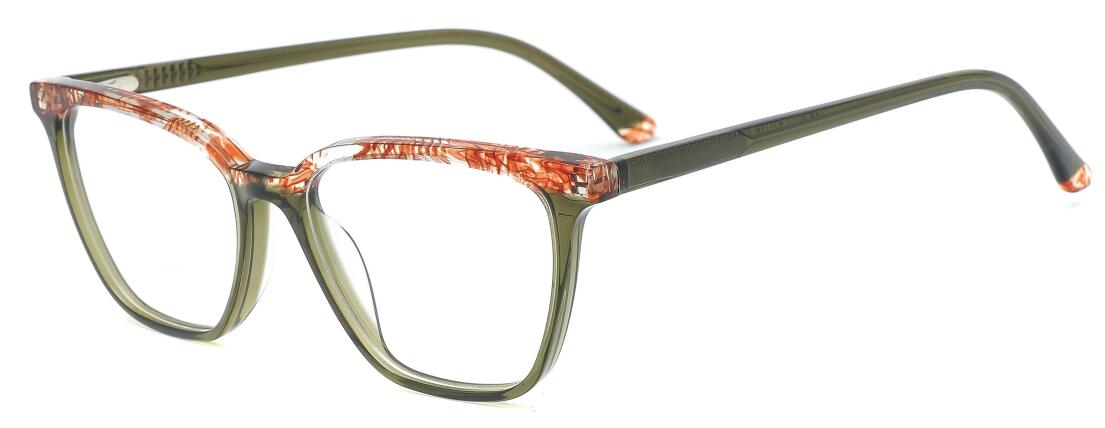
Thanks for reading.
Sophie Yang
004@mikeeyewear.com